

Typically, the profiler has software to predict the drawn fiber’s cutoff wavelength, MFD, and NA. This is critical information to analyze the completed preform and predict the ability to meet design goals. The preform profiler is critical to meeting design goalsĪs an MCVD operator, you rely on the profiler to measure the completed preform’s refractive index and dimensions, such as the thickness of glass layers. The following paragraphs offer a high-level review of critical design goals for optical fiber preforms, along with tips for MCVD operators to manufacture the specified glass waveguides and achieve reproducible designs. In addition to resolving design issues with the designer, the MCVD operator must tightly control multiple equipment and process variables throughout the fabrication process. The “blueprint” may look great on paper, yet the two professionals need to work closely together to figure out real-world specifics. In fact, the preform fabrication’s designer/operator team is similar to how architects and homebuilders work together. In my years of operating and maintaining an MCVD fabrication system at 3M, I worked closely with the designers and was intimately involved in the design process to ensure designs were manufacturable in regard to expansion coefficients and so forth. Additional waveguide design fabrication goals include high purity, low OH, uniformity, and reproducibility. In addition, there are many design tactics to meet cutoff wavelength, mode field diameter (MFD), and numerical aperture (NA). Low metallic impurities prevent reflective loses, and dry raw materials prevent absorptions. It uses closed circuit control logic to enable the machine to perform safely.As we all know, high-purity raw materials are critical to achieve design goals. Each oven can be loaded and unloaded independent of the other ovens.Ī PLC is used to control the actuators. Preforms are loaded and unloaded automatically. In case of breakage, the system allows for the broken material to be removed. The outer surface of the preform is protected from contamination. The housing is a stainless steel cylinder.
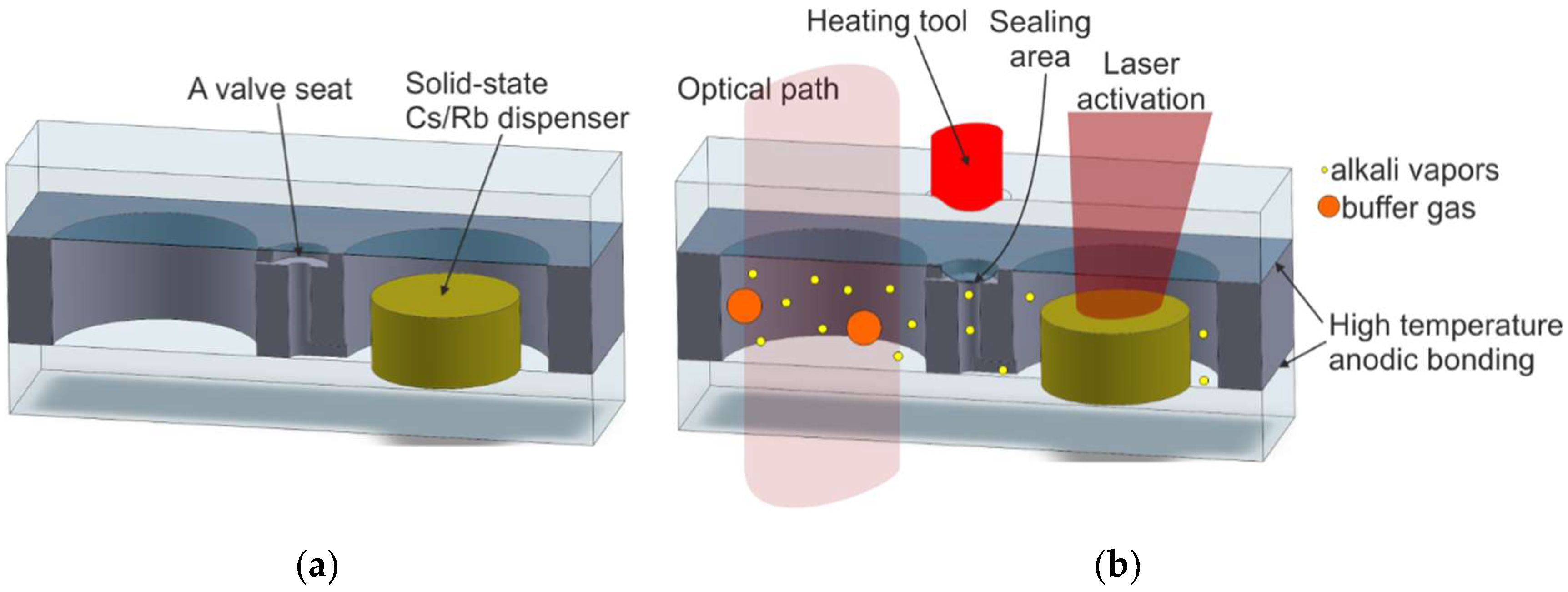
The ovens consist of 3 cylindrical units for core soaking and 5 cylindrical units for clad soaking. The small frame sits on a table on the Y-axis and Z-axis linear rails. The top section contains the vertical actuator and gripper. The frame consists of two parts, a large base section which contains the ovens and load station, and a top section for loading. The structure is manufactured for strength and flexibility. The Preform Soaking Oven systems are comprised of four main parts, a main structure, ovens, a preform movement system, and a process control subsystem. If the Preform Soaking Oven is not used, it could take days or even weeks for the excess gas to escape at ambient temperature.Ī further benefit of using the Preform Soaking Oven is a potential reduction in draw ramp up time since the glass preforms can be brought to the draw furnace already warm, reducing the time to bring the preform up to temperature at the draw tower.Įach Preform Soaking Oven is configured with 3 or 5 ovens which operate independently of each other. Excess gas which is invisible to the naked eye, can cause bubble formation in the glass resulting in fiber breaks during the draw process, if not removed from the glass preform. This system is used to heat glass preforms after they have been sintered enabling excess gas still trapped in the preform after sintering to escape.

The Preform Soaking Oven System is designed and manufactured by ASI/Silica Machinery, LLC.
